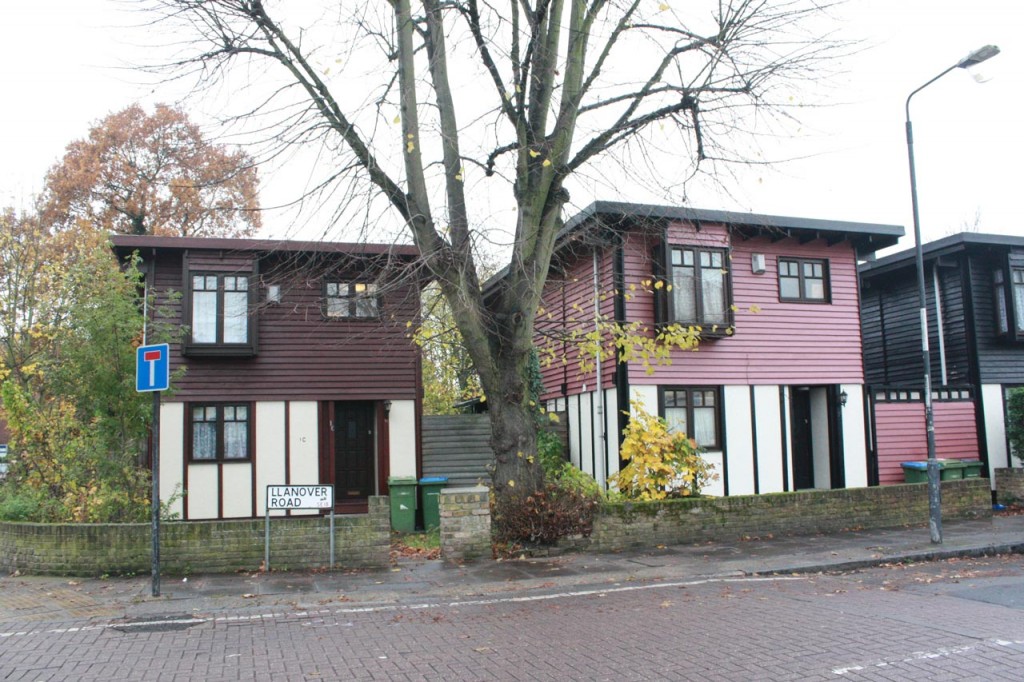
While walking along Herbert Road photographing buildings of local interest, I walked right past some of the most interesting – the group of 5 wooden-framed houses at the top of Llanover Road. These houses were built by the people who lived in them as part of a cooperative self-build group, following a design by the architect Walter Segal. Some of the builders still live there, and I was lucky to be able to talk to a couple of self-builders, Gordon and Dee, about how they did it. They generously lent me their album of photos recording the build – some of them are included below.
Walter Segal was a German-born architect who moved to London in 1936. In 1963 he pioneered his eponymous building method when he constructed a “temporary” wood-framed building in a back garden in Highgate to house his extended family while their main home was being extended. That building is still standing today, the first of many constructed using the Segal method. Quite a few Segal houses have been built in south-east London, and those in Lewisham are particularly well known. The architect himself provided guidance and encouragement to the Lewisham builders. After he died in 1985 two of the roads where his houses stand were named after him: Walters Way in Honor Oak and Segal Close near Blyth Hill. Two of the houses in Walters Way were open to the public in last year’s London Open House, whose brochure described them as:
Each house is unique, many extended and built using a method developed by Walter Segal, who led the project in the 1980s. Both houses have benefitted from extensions and renovations. Sustainable features include solar electric. water and space heating. Walter Segal 1987.
There’s more about the green and sustainable features on the Superhomes web site, and the Modern House web site has some great photographs and details of several South London Segal houses.
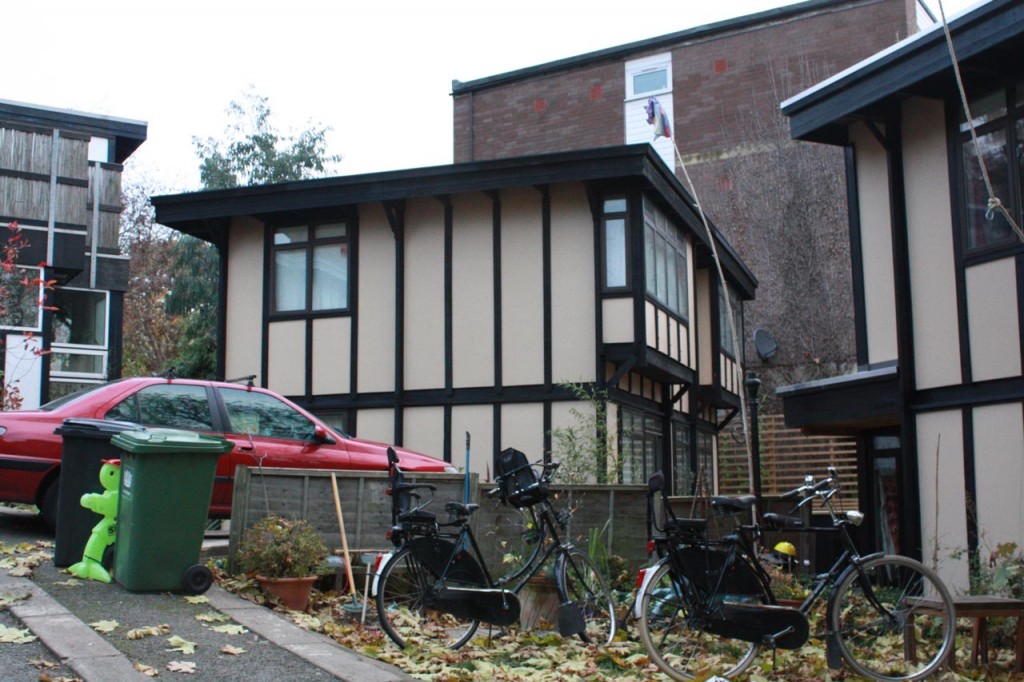
Walter Segal’s method was designed to be simple, suitable for people with no previous building experience, and to avoid what he called the “tyranny of wet trades”; that is, there is no need for brick laying or plastering. The building plan is based on a set of timber frames, constructed from standard, readily available materials using basic carpentry skills, which sit on pad foundations. This means that there is less need for levelling a site and disrupting existing trees and vegetation, and it allows houses to be erected on sloping sites which are problematic for traditional methods: Walters Way, for example, is a steeply sloping site. The roof is attached after the frames have been erected, allowing the builders to work under cover on the rest of the building. Within the grid defined by the wooden frames builders can chose the layout of the rooms in the house and, as the walls are not load bearing, can even rearrange the internal lay-out after the build is complete.
In the borough of Greenwich a number of Segal self build developments were overseen by Co-operative Housing in South-East London (CHISEL). Gordon and Dee were part of the first of these: the Greenwich Self Build co-operative project at Llanover Road, which officially started on 16th March 1993. The site had been occupied by a row of three Victorian houses, numbers 220 to 224 Herbert Road, according to the 1914 OS map, though they had been demolished and the site littered by fly-tipping by the time the project started. The first of Gordon and Dee’s photos below show the site as it was when they started. The fly-tipping and rubbish had been cleared away by the council – the only physical help the council contributed to the build! The self-builders had all been selected by the council, and were working on a “Self Build For Rent” model. They committed to putting in 20 hours a week each on the build. In return for their labour in building the houses they would be able to live in them on a reduced rent. Before starting they attended a training course, though it mainly seems to have covered how to use power tools safely.
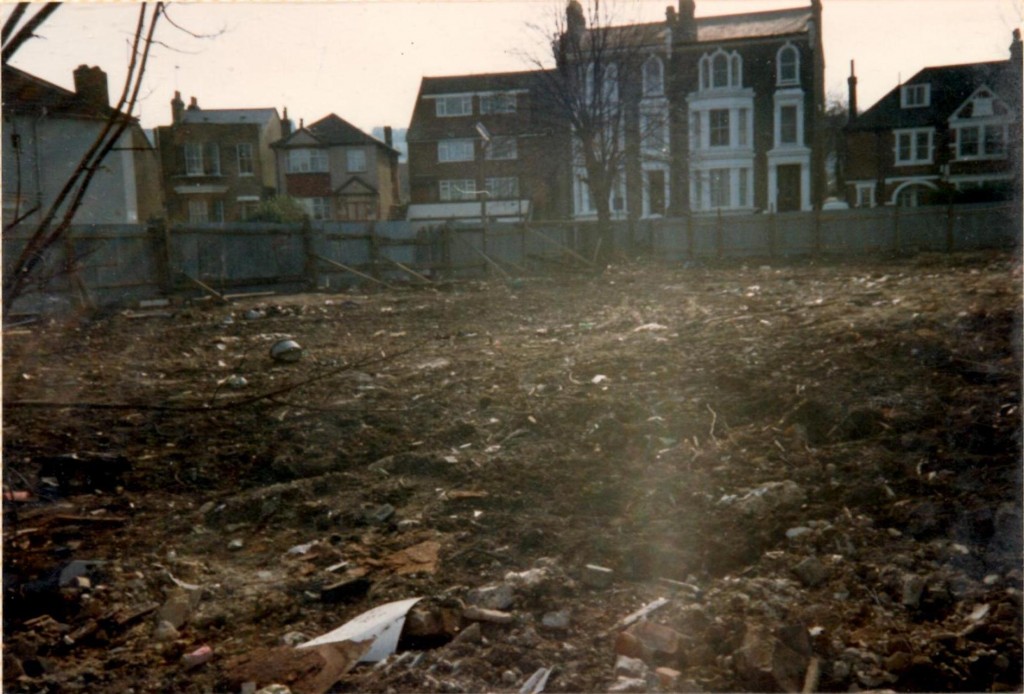
The official start was attended by local MP Nick Raynsford, seen on the left in the photo below. The architects were probably Architype, led by Jon Broome, who also worked on the other projects undertaken by the Greenwich Self Build co-operative at Parish Wharf near Woolwich Dockyard, and Birchdene and Silver Birch in Thamesmead.
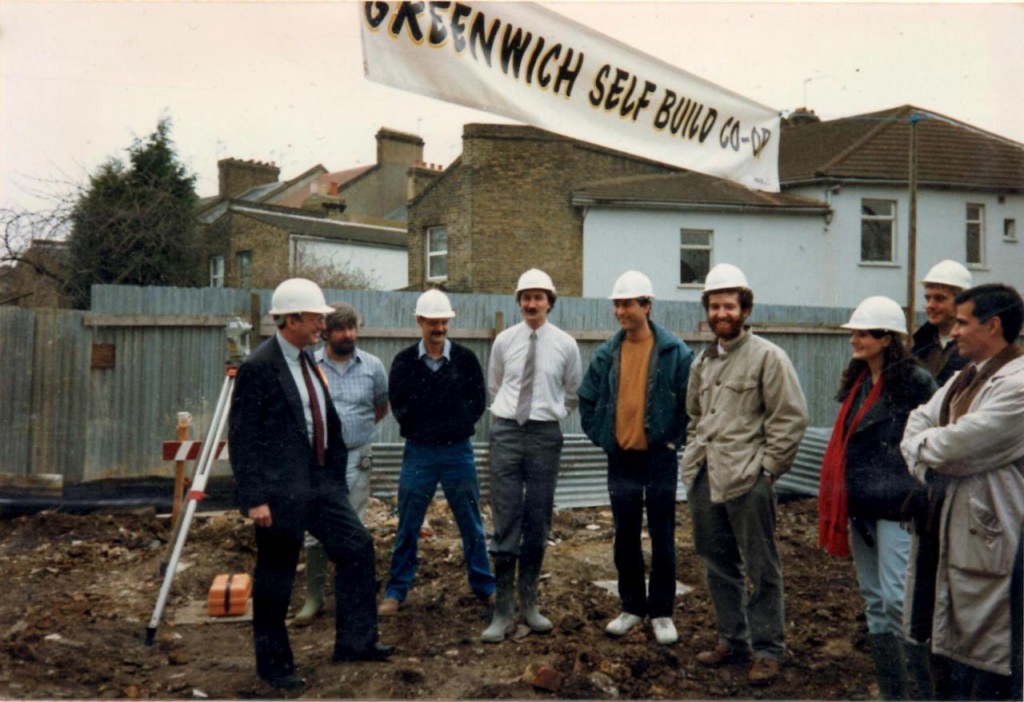
The first stage of the build was to dig the holes for the concrete bases for the pad foundations. The little digger in the photograph was the only “large” piece of machinery used in the whole build, and was passed on the next Greenwich project at Parish Wharf when the Llanover Road builders had finished with it.
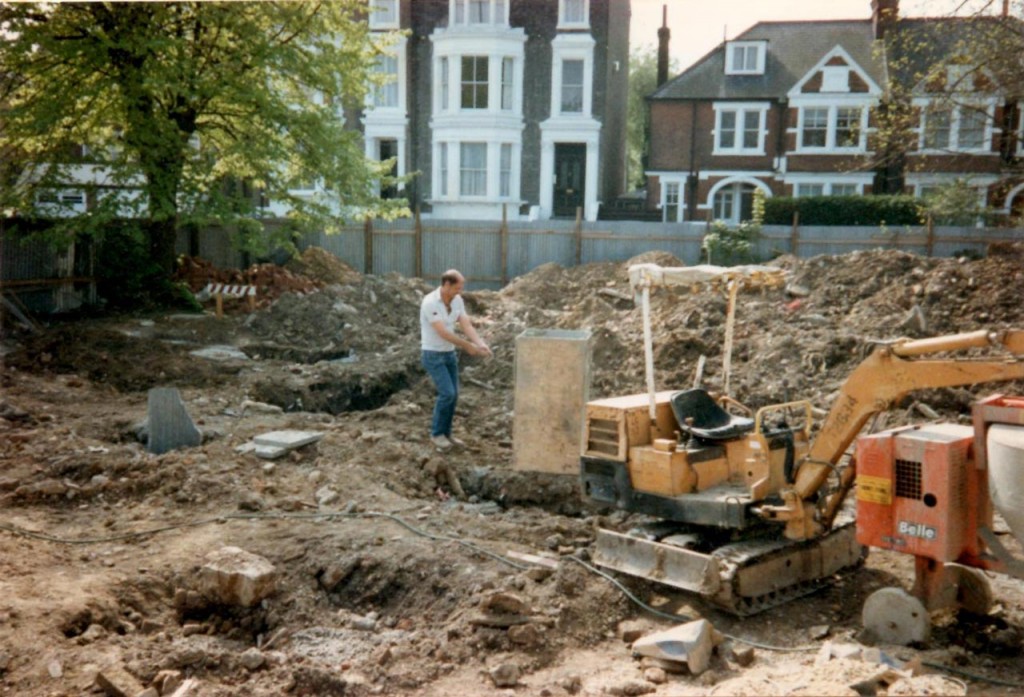
Unlike brick built houses, the foundations of Segal houses don’t run underneath the entire area of the house. Instead they have pad foundations – the upright posts of the wooden frames stand on a paving slab which is sitting on top of a point block of concrete, about 600 x 600 wide, the depth depending on local soil conditions. The ends of the wooden beams are sealed with a lead sheet which seals them very effectively against moisture. The weight of the house holds it in place. For the Llanover Road houses the flat felt roof is topped with some two and a half tons of gravel, so there is quite a weight to keep the house in place. The only connection to the ground is through services pipes and cables. In Gordon and Dee’s experience there has never been any problem with stability, even in the recent strong storms which damaged more traditionally built properties. They did say that the house sometimes sways a little though.
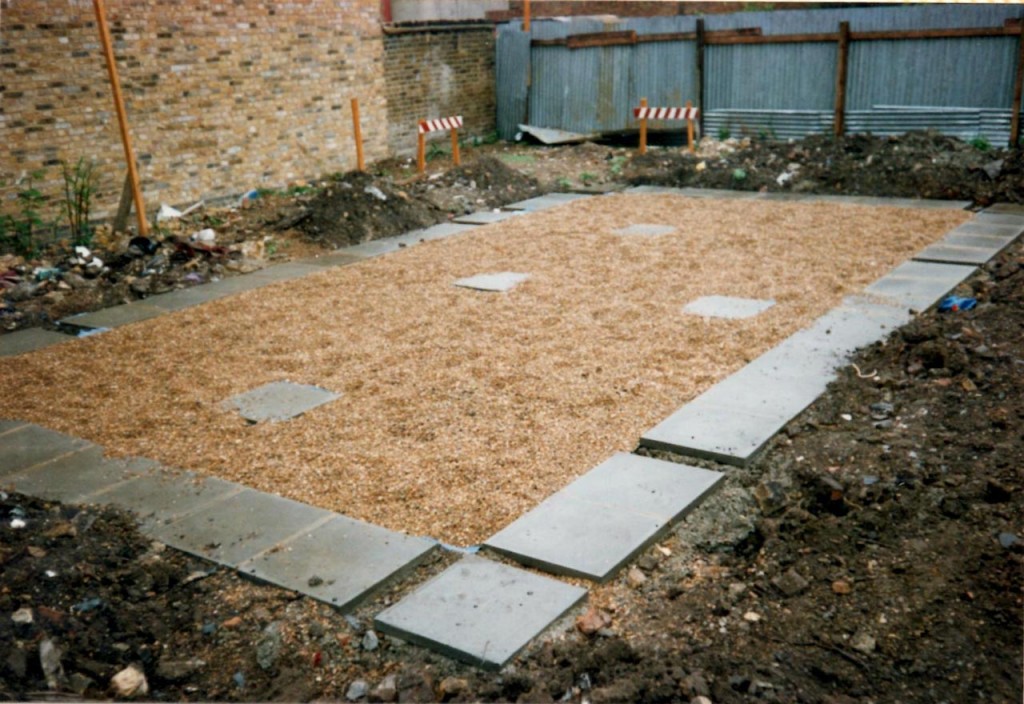
In the early parts of the work at Llanover Road all of the self builders worked together – preparing the foundation bases and constructing and erecting the frames and main structure. After that they tended to concentrate on their own properties. It was a lot of work, especially while holding down a job and bringing up a family
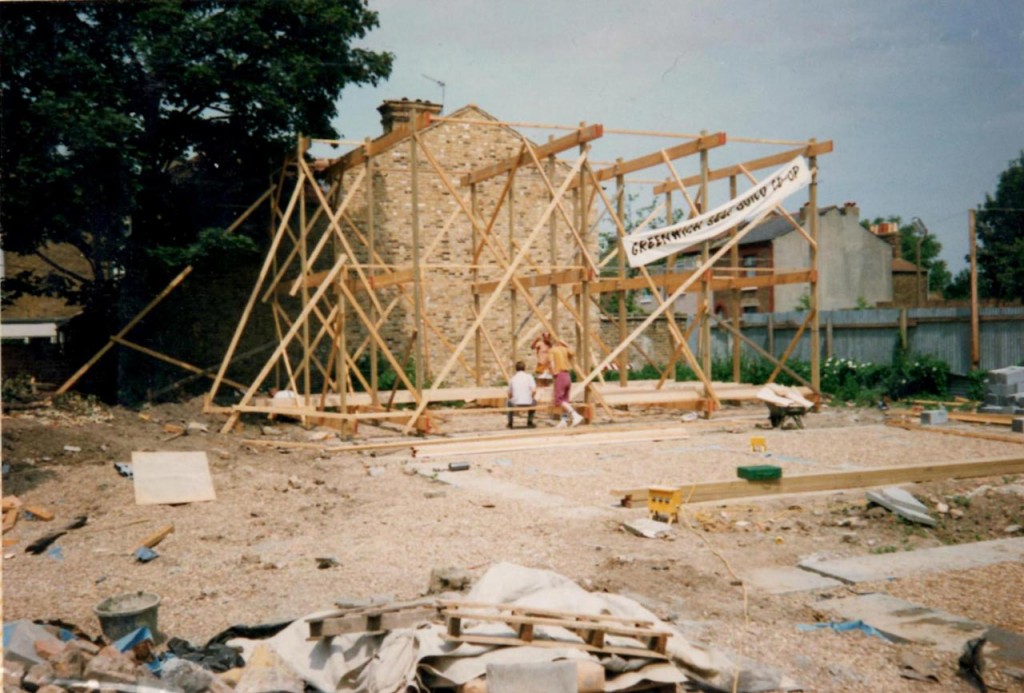

The roof in the standard Segal design is flat, though with some critical differences to other flat roofs to avoid some of their problems. The waterproof membrane is not fixed down but laid loose on the roof deck, with a generous amount of overhang, like a table cloth. This allows the membrane to accommodate any movements in the building frame and to expand and contract with temperature, so it doesn’t crack or tear like fixed membranes. On top of the membrane is a 40mm layer of 20mm diameter shingle, which weighs it down and shields the membrane from direct sunlight. The Llanover Road houses had the standard Segal design flat roof, though the other Greenwich properties had pitched roofs. For the Llanover self builders the only way to get the shingle up on to the roof was to use a rope and pulley and a builders’ bucket. Shifting two and a half tons of shingle in this way was a significant undertaking!
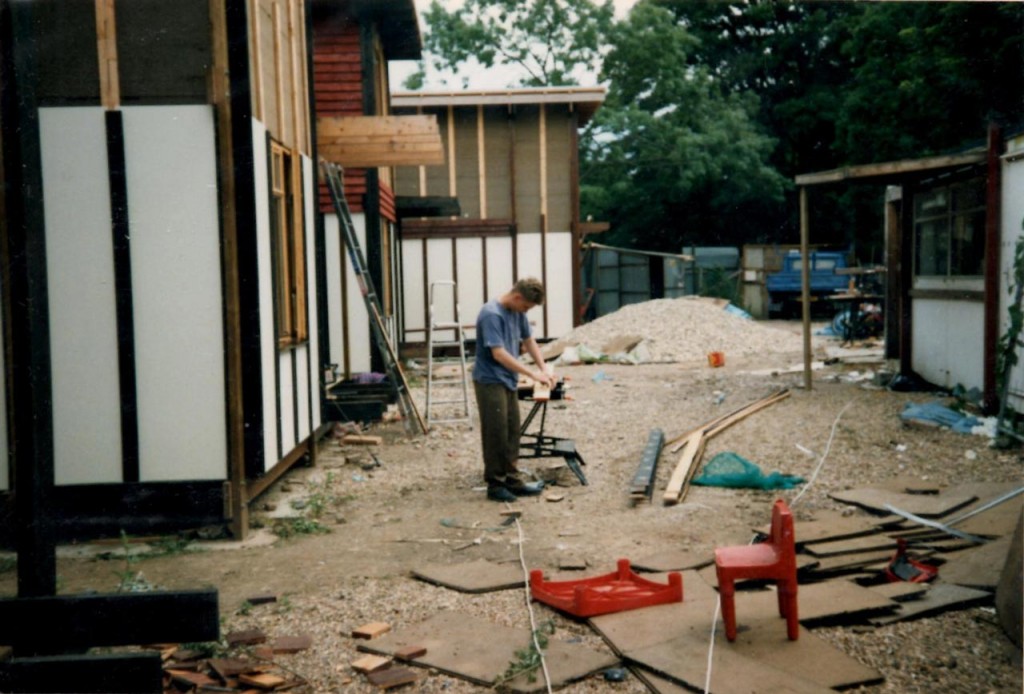
The internal timbers all had to have six coats of a special varnish. The walls and partitions were constructed with cavities, which were filled with insulation made from recycled copies of Yellow Pages using a blowing machine – one of the reasons the Segal homes are more energy efficient than other houses. The trickiest carpentry inside the house was needed to construct the stairs, especially the different shapes required for the treads when the stairs turned a corner.
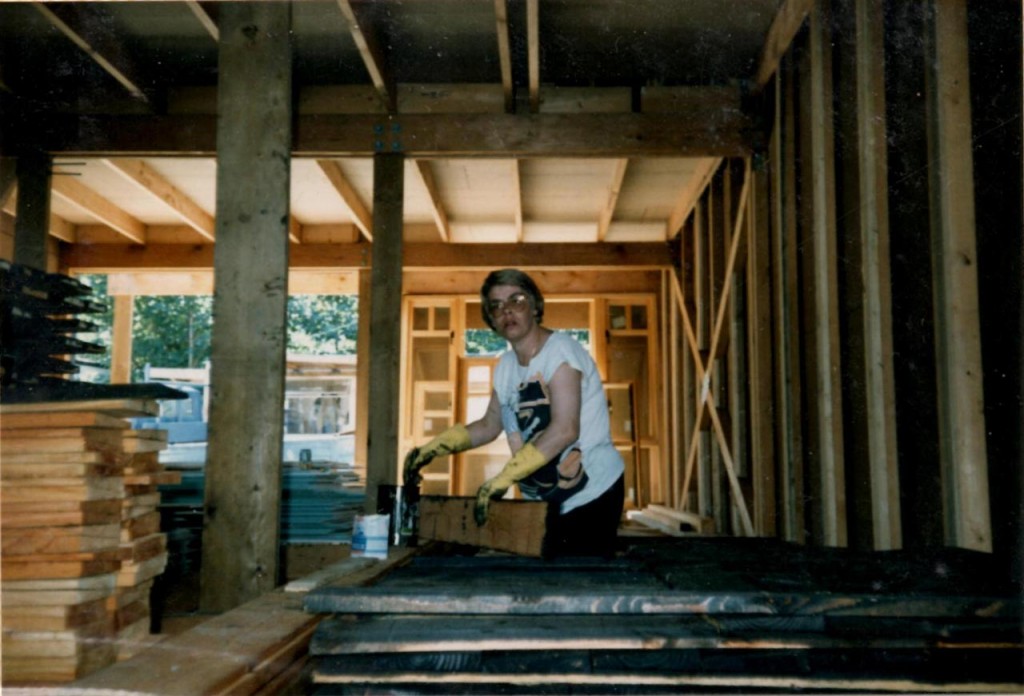
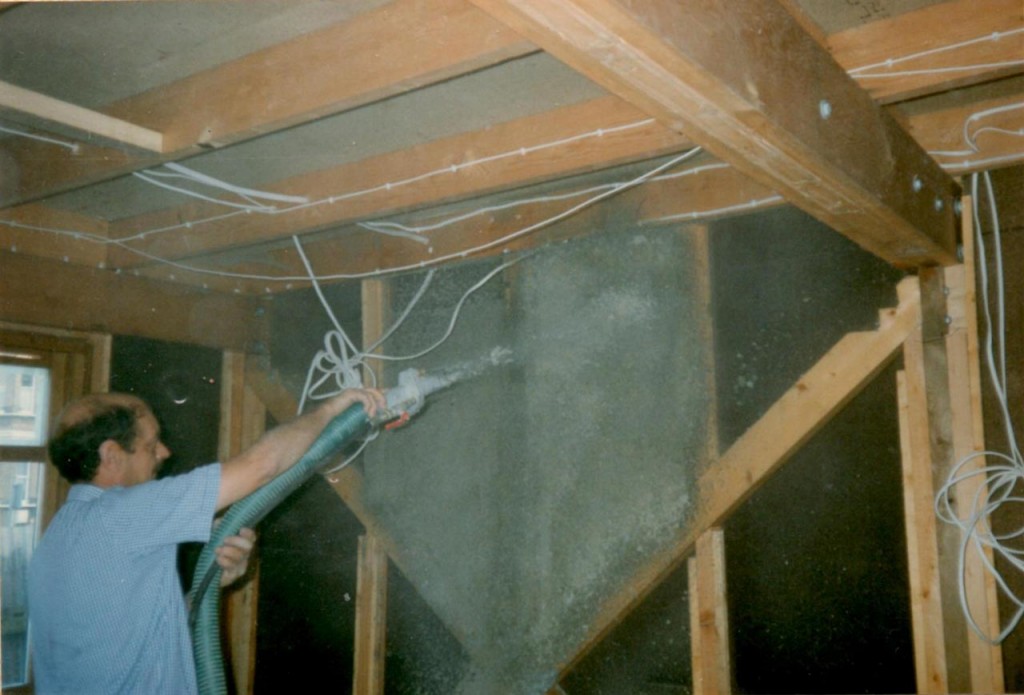
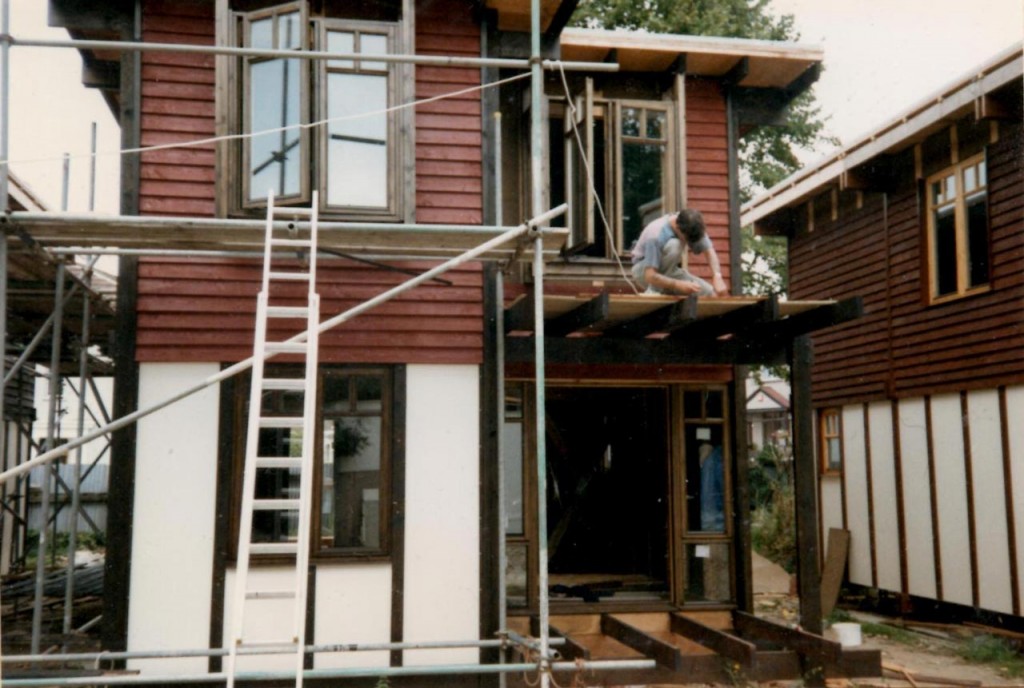
It took two years and nine months to complete the Llanover Road self build, and the material costs for a house were £13,500. The development was the first Segal housing project to be completed since the original ones in Lewisham. The opening ceremony was again attended by local MP Nick Raynsford, who was also the Labour Party Housing Spokesman. Inside, the completed Segal house feels surprisingly spacious. If the beams are left exposed it has an Elizabethan feel, though many self-builders paint the insides a uniform colour, making it feel like any other house.
The Greenwich Self Build co-operative went on to further Segal projects in Woolwich and Thamesmead, with the members of the original group maintaining their involvement for later developments. The Parish Wharf development is described in English Heritage’s Survey of London volume about Woolwich as follows:
Parish Wharf, off Woodhill, is of the same period, but it is something different. The self-build method espoused by Walter Segal was followed here in 1992–5 to produce eight free-standing four-bedroom houses. Using modular, dry-jointed and cheap post-and-beam timber frames, on stilts to avoid the cost of foundations, these chalet-like houses were built for themselves by members of Co-operative Housing in South-East London (CHISEL). Their architects were Architype, then led by Jon Broome, Segal’s leading disciple, with Bob Hayes as the job architect. The name, which seems puzzling here on the landward side of the railway, reprises that of a municipal depot that lay east of the former dockyard.
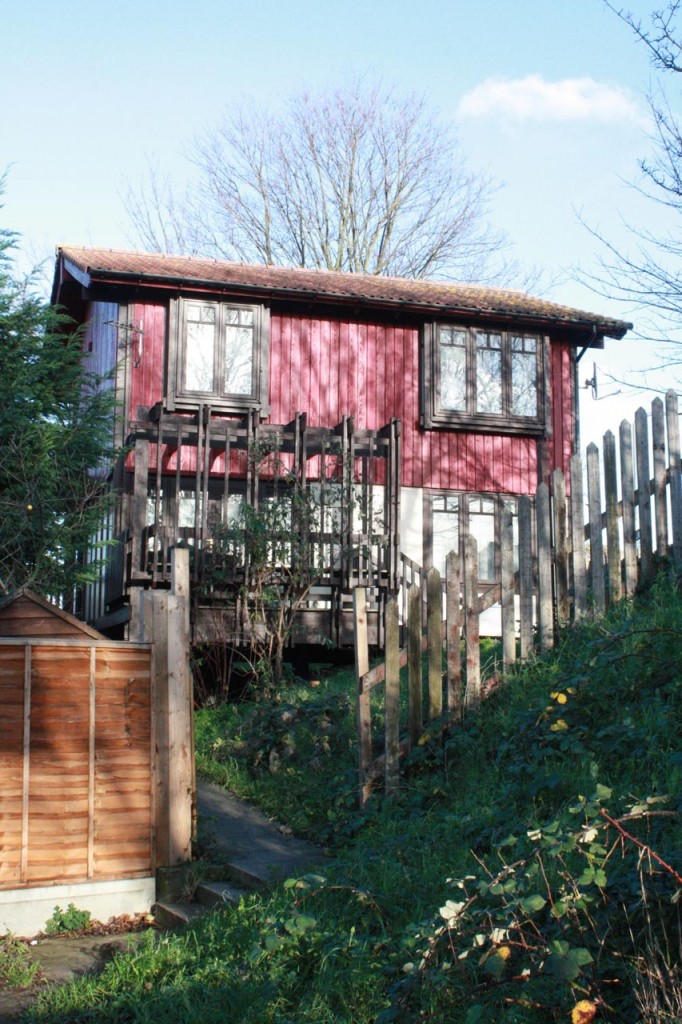
As well as the Llanover Road, Parish Wharf, Birchdene and Silver Birch projects the Greenwich Self Build co-operative put in a proposal for a further Segal project in Abbey Wood, but it didn’t get the go-ahead. The co-operative was formally dissolved just a couple of years ago, in September 2011. Co-operative Housing in South-East London (CHISEL) is responsible for about 250 homes in south-east London, Colchester and Brighton, of which about a third are self-build, energy efficient Walter Segal properties that were constructed by the tenants who mostly still live in them.
Gordon and Dee still live in the house they built themselves, 20 years ago. As the name they gave their house attests, they don’t have any burning desire to build another house.
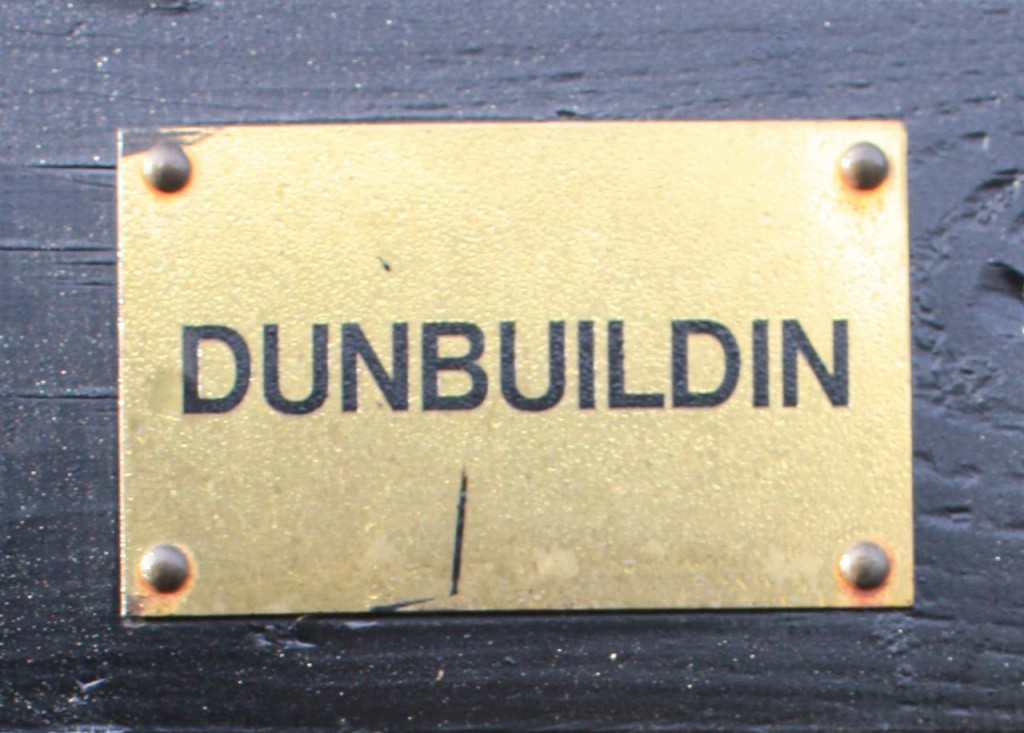